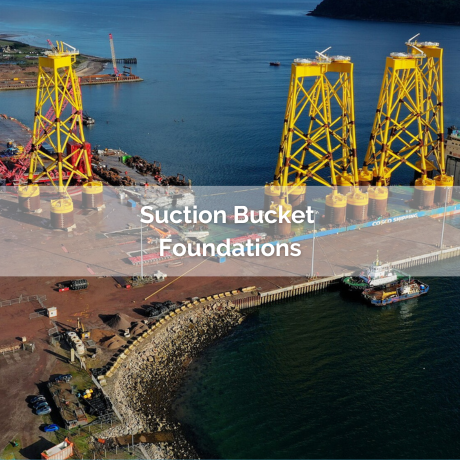
Suction Bucket Foundations
Whilst monopile foundations are certainly the most common type of foundation for offshore wind farms globally, they are not always a suitable option due to environmental or site conditions. Suction bucket jackets – also known as caissons – are fast becoming a popular alternative where seabed conditions allow.
Suction bucket jackets work using the principles of suction instead of driven piles into the seabed and are installed without the use of mechanical force. They have either 3 or 4 legs like a standard jacket, giving the wind turbine much more stability compared to a monopile. A monopile is simply a singular pile, drilled or driven into the seabed, and so levering the whole weight of the wind turbine on a single point. The ‘top half’ of a turbine is heavy, with the tower, transition piece, nacelle and blades. A suction bucket solution is particularly suitable for areas which experience severe weather conditions such as typhoons, as in Taiwan. This island nation has excellent wind speeds for wind energy on ‘normal’ days, but with the unpredictability of extreme high winds.
The first Taiwanese wind farm that uses suction bucket foundations is currently under pre-construction. If this goes well, it could influence future wind farm installations in the region – and other parts of the world where tricky weather conditions or environmental factors persist and site conditions allow.
On the other side of the globe, earlier this year, our FoundOcean engineers and technicians were grouting the world’s deepest offshore wind turbine, using suction bucket jacket foundations, on SSE’s Seagreen wind farm, Scotland’s largest offshore wind farm – 114 turbines powering more than 1.6 million homes.
Oliver & Yau Collins.
Taiwan is currently ramping up their wind industry in order to meet their ambitious 2030 targets. Listening to the presentations at Energy Taiwan, I was impressed with their aims but thought that their focus on ‘local content’ could make their renewables target even more challenging.
A key positive of suction bucket jackets is the speedy installation process, with no pre-piling required. One set of suction bucket jacket foundations can be completed in 24 hours – a single day per turbine location.
For a typical pre-piled jacket foundation, there is an initial piling campaign where 3 or 4 piles are driven with the help of a pile template. Following this campaign, a second campaign will install the jacket. The single installation process required for suction bucket foundations is more efficient if the developer is having to deal with erratic weather windows, like in Taiwan.
Oliver and Yau at Energy Taiwan Expo 2023.
This faster installation process is ideal in areas which have pile-driving bans at particular times of the year or times of day. Restrictions are put in place due to the noise or vibration levels and the effect that the piling process could have on the feeding habits or migration or mating seasons of marine life. The suction bucket installation process is much quieter and more environmentally sensitive compared to the noise and vibration of traditional piling.
The method of securing suction bucket jackets means that they are used in locations with a softer seabed. Because of their size, they also have a much bigger surface area than other types of foundation solution and therefore a larger area of clear and suitable seabed is required. Each bucket could be up to 14m in diameter, so the overall footprint required for each turbine might be 56m in diameter. This does result in more scour protection being needed for this type of foundation.
Oliver delivering his presentation at Energy Taiwan Expo 2023.
To install a suction bucket jacket, the jacket is lowered onto the seabed. Then negative pressure is created inside the caisson by pumping water out. In layman's terms, as the negative pressure within the void increases due to the water being sucked out, the caisson void tries to re-establish equilibrium. Unable to replace the water that has been removed, it instead reduces the volume by effectively pulling the foundation down into the seabed, helped on its way by the weight of the structure. The void remaining after the suction process is then filled with ultra-low strength grout.
The cost-savings for the customer in terms of grouting can be significant because, although the actual volume of grout is more, the yield for an ultra-low-strength formula used in suction bucket foundations could be 5 times as much as a typical construction grout. The grout can be designed to meet project-specific requirements, i.e. faster-setting or slower-setting formulations. The grout designs can be infinitely varied. An additional benefit in using an ultra-low strength grout is that the end-of-life recovery and cleaning process of the foundation can be much easier.
At FoundOcean, we are eagerly following the progress of Taiwan’s first suction bucket foundation wind farm and it will be interesting to see which other countries opt for this method in the coming years.
For more information on FoundOcean’s experience and capabilities, contact the team on +44 1506 440330 or email info@foundocean.com